- Интервью
- Отчеты о конференциях
- Цифровая трансформация
- Электронный документооборот
- Финансы: стратегия и тактика
- Общие центры обслуживания
- Информационные технологии
- Финансовая отчетность
- Риск-менеджмент
- Технологии управления
- Банки и страхование
- Кадровый рынок и управление персоналом
- Управление знаниями
- White Papers
- Финансы и государство
- CFO-прогноз
- Карьера и дети
- CFO Style
- Советы по выступлению на конференциях
- Обзоры деловых книг и журналов
- История финансов
- Свободное время
- Цитаты
КОНФЕРЕНЦИИ
-
8 апреля 2025 года
Москва -
10-11 апреля 2025 года
Москва -
18 апреля 2025 года
Москва -
22-23 апреля 2025 года
Москва -
24 апреля 2025 года
Москва -
15-16 мая 2025 года
Москва
Алексей Черноплеков, «ЕвроХим»: «Мы идем к цели НОЛЬ - ноль травм, ноль аварий, ноль внеплановых потерь»
01.04.2025
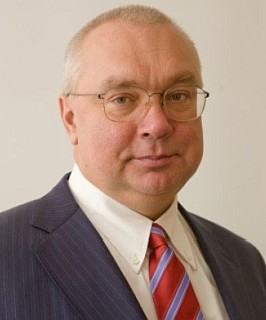
Справка о компании: «ЕвроХим» является крупнейшим в России производителем минеральных удобрений. По объёму производства компания «ЕвроХим» входит в тройку европейских и десятку мировых производителей химических удобрений. «ЕвроХим» объединяет 6 добывающих и производственных предприятий, выпускающих удобрения, продукцию органического синтеза, минеральное сырье, кормовые фосфаты, а также транспортные подразделения и широкую сбытовую сеть в России и за рубежом.
Безопасность производства. Цель 000
Статья посвящена включению в управление предприятием производственных целей в области безопасности – управлению производственными рисками. Речь пойдет о ситуациях на эксплуатируемых или проектируемых производствах, которые могут причинить вред людям, окружающей среде и сопутствующий вред бизнесу.
В сфере безопасности мы руководствуемся четкой целью – НОЛЬ. Это означает ноль травм, ноль аварий, ноль внеплановых потерь. При этом мы реалистично подходим к оценке ситуации: любое отклонение от нормы рассматривается как естественное явление, подчиняющееся законам природы.
Отмечу также, что наш подход к безопасности требует координации с другими подразделениями для достижения оптимальных результатов в работе.
Такой комплексный взгляд на безопасность позволяет нам защищать персонал, сохранять окружающую среду, поддерживать стабильность бизнеса и обеспечивать устойчивое развитие производства. Это направление работы является одним из ключевых приоритетов нашей компании, требующим постоянного внимания и совершенствования.
Физические основы достижения цели 000
Специалисты в области промышленной безопасности хорошо знакомы с пирамидой несчастных случаев, показанной на рисунке. Идеальная картина – штатный режим работы: оборудование функционирует исправно, персонал действует согласно инструкциям, технологический процесс протекает без отклонений. Однако реальность далека от идеала. Как же предупредить инциденты?
Необходимо помнить, что на пути к аварии всегда возникают предвестники: выходы за нормы технологического режима, отказы оборудования, опасные действия и опасные условия. Ключевую роль здесь играют барьеры безопасности – защитные меры и элементы производственной системы, предотвращающие риски или минимизирующие последствия их реализации. Постепенный отказ этих барьеров, начинающийся с незначительных отклонений, приводит к нарастанию риска, потере контроля над ситуацией и, в конечном итоге, к аварии или даже катастрофе.
Принципы управления рисками безопасности химических производств
Цель 000 достижима различными путями. Традиционно успех связывался со строгим следованием предписаниям и правилам. Однако, катастрофы, подобные пожару на платформе Piper Alpha в 1988 году и взрыву Deepwater Horizon в 2010 году, показали ограниченность этого подхода. Разлив миллиона тонн нефти в Мексиканском заливе наглядно продемонстрировал, что даже безупречное соблюдение правил не гарантирует безопасности. Эти события подчеркнули необходимость поиска новых, более эффективных способов достижения цели 000, выходящих за рамки простого следования предписаниям.
Существующие методы обеспечения безопасности производства не всегда эффективно интегрируются в бизнес-процессы. Необходимо учитывать потенциальные потери, определяя максимально допустимые, и принимать соответствующие управленческие решения. Традиционный подход фокусируется на строгом соблюдении установленных норм безопасности, предполагая, что ответственное отношение исключает аварии. Однако практика показывает, что даже при безупречном выполнении правил, риск происшествий сохраняется. Именно этот факт, особенно ярко проявившийся после крупных аварий, привел к разработке новых методов.
Например, эмпирический подход предполагает выявление ключевых рисков посредством междисциплинарной экспертизы и создание дополнительных мер безопасности.
Однако понимание физики процессов требует большего - необходим онлайн сбор данных о состоянии оборудования, материальных потоков и деятельности персонала, что позволяет выявлять предвестники аварийных ситуаций и измерять риск в режиме реального времени, принимая превентивные меры. Этот подход, сосредоточенный на конкретной области, органично встраивается в стандартные бизнес-процессы принятия решений (в отличие от «голого» соблюдения требований)
Управление рисками безопасности производств осуществляется на оперативном (начальник смены), тактическом (начальник цеха) и стратегическом (управляющие бизнесом) уровнях управления. Любая производственная цель (объем продукции, качество продукции, эффективность производства и безопасность) каскадируется сверху вниз, доводится до каждого уровня управления.
Вызовы для управления рисками безопасности производств онлайн
Основная сложность для нас в обеспечении безопасности – автоматизированный сбор данных о текущем состоянии производства. В отличие от технологических систем, где мы успешно отслеживаем температуру, давление и другие параметры, получение информации о состоянии персонала, прежде всего – аппаратчиков, сопряжено с трудностями. Сейчас данные о надежности оборудования поступают с задержкой в 4-5 дней, хотя экспресс-методы, такие как вибро- и акустическая диагностика, используются для критически важных элементов.
Для решения этой проблемы мы разработали два метода. Первый – использование голосового помощника, аналогично практике в военных системах, обеспечивающего пошаговое руководство оператором и постоянную обратную связь. Оператор проговаривает каждый этап работы, получая подтверждение и корректировки на основе данных из других систем мониторинга. Например, после сообщения о выполненном заземлении система проверяет данные датчиков и указывает на ошибки, если таковые имеются. Второй метод – видеофиксация с последующим распознаванием изображений.
Дашборд мастера/начальника смены для управления рисками безопасности производств на оперативном уровне
Сейчас мы разрабатываем пилотный проект – дашборд мастера/начальника смены, предназначенный для управления производственными рисками. Интерфейс дашборда лаконичен: черный экран, активизирующийся при возникновении угроз. В случае повышения уровня риска, экран подсвечивается, отображая динамику изменения риска по трем ключевым показателям: прогнозируемая травматизм /смертность, а также упущенный маржинальный доход.
Дашборд предоставляет руководителю смены информацию в двух панелях. На левой панели – детализация причин повышения риска (выявленные нарушения барьеров безопасности, неисправности оборудования и другие дефекты). Информация предоставляется на ранней стадии, до возникновения аварийной ситуации. На правой – прогноз последствий растущих индивидуальных рисков, позволяющий оценить значимостью угрозы.
Под обеими панелями отображаются рекомендации (лучшие практики отрасли) по предотвращению эскалации ситуации и минимизации рисков в возникающей конкретной ситуации.
Наш опыт в промышленном производстве, особенно в синтезе аммиака (технология которого унифицирована на трех наших предприятиях), позволяет нам глубоко понимать процессы, выявлять потенциальные проблемы и разрабатывать эффективные решения. Это понимание критически важно для повышения безопасности. Система предупреждения о рисках помогает операторам, начиная от простых ограничений доступа и эвакуации персонала, до сложных мер предотвращения аварий. Ключевой момент – принятие решения о разгрузке или остановке установки. Для мастера смены это сложнейшая дилемма: остановка означает потерю бонуса или зарплаты, а продолжение работы – риск аварии с угрозой для жизни людей.
Цифровой двойник рисков
Для обеспечения безопасности на всех этапах производства необходимо обрабатывать, и обрабатывать быстро, большой объём данных о текущих процессах и показателях безопасности. Нами разрабатывается система, которую разумно называть Цифровым двойником рисков, для комплексного мониторинга и управления этими данными.
Цифровой двойник рисков (ЦДР) безопасности производства – это программное обеспечение, реализующее на компьютерах вычислительно-логические алгоритмы математической модели процесса удержания и потери удержания энергии и материалов конкретного производства. Она построена из изученных элементов, созданных на основе физических принципов и законов природы.
Благодаря этому программное обеспечение обладает способностью с контролируемой неопределённостью рассчитывать индивидуальные риски и показатели безопасности конкретного производства (то есть преобразовывать состояния производства в показатели безопасности производства).
Производственная безопасность – это симбиоз человеческого опыта и искусственного интеллекта. На базовом уровне роботы и автоматизированные системы выполняют функцию контроля и предоставляют операторам подсказки. Однако на стратегическом уровне, где принимаются решения, критична человеческая способность анализировать множество вариантов, учитывая не только безопасность, но и экономические показатели (объём, качество, затраты). Полная алгоритмизация этого процесса сегодня пока невозможна, но интеллектуальные системы уже эффективно помогают в принятии оптимальных решений.
Алексей Черноплеков, руководитель проектного офиса по управлению рисками, «ЕвроХим»
Наши конференции:
- Восьмая конференция «Управление рисками в промышленности»
- Сорок пятая конференция «Эволюция клиентского сервиса в ОЦО: от сервисного подразделения до стратегического бизнес-партнера»
- Двадцать шестая конференция «Корпоративное налоговое планирование»
- Сорок четвертая конференция «Команды и процессы в ОЦО: инновационные подходы к управлению»
- Четырнадцатая конференция «Управление дебиторской задолженностью»
- Двадцать седьмая конференция «Корпоративное налоговое планирование. Актуальные налоговые споры-2025»
- Третья конференция «Цифровизация финансового рынка в России: тренды и перспективы развития»
- Сорок третья конференция «Цифровые ОЦО: синергия команд, технологий и сервиса»
- Тринадцатая конференция «Управление дебиторской задолженностью»
- Двадцатая конференция «Автоматизация корпоративных бизнес-процессов»
Комментарии