- Книжный клуб: рецензии, анонсы, встречи
- Колонка руководителя
- Корпоративные финансы
- Менеджмент и маркетинг
- Поездки
- Управление результативностью
- Финансы за пределами цифр
- Финансы и Менеджмент
КОНФЕРЕНЦИИ
-
2 декабря 2024 года по 27 марта 2025 года
Москва -
2 апреля 2025 года
Москва -
8 апреля 2025 года
Москва -
10-11 апреля 2025 года
Москва -
18 апреля 2025 года
Москва -
22-23 апреля 2025 года
Москва
Обучение элементу «Устранение потерь по каждому рабочему месту» в ПАО «ОАК»
07.10.2016
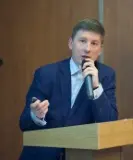
В 2016 году Объединенной авиастроительной корпорации исполняется 10 лет, и в течение 8 из них компания работает над внедрением и развитием собственной производственной системы, направленной на развитие корпоративной культуры, повышение операционной эффективности и конкурентоспособности производств, закрепление лучших практик и стандартов как на производственном, так и на управленческом уровне.
«Наша цель – быть корпорацией мирового уровня для наших акционеров, заказчиков, работников и для всех заинтересованных партнеров», – подчеркнул президент, председатель правления ПАО «ОАК» Юрий Борисович Слюсарь.
Производственная система ОАК развивается на всех дочерних зависимых обществах в соответствии с дорожной картой внедрения. В рамках этого процесса проводится обучение инструментам Бережливого производства, внедрение практик эффективной организации процессов, закрепление философии непрерывных улучшений, заложенной еще компанией «Тойота».
Сущность производственной системы Тойота – деятельность по повышению эффективности производства через ликвидацию потерь в рабочем процессе и обеспечение простоты выполнения операций.
Без освоения элемента «Устранение потерь по каждому рабочему месту», действия, направленные на организацию / оптимизацию производственных потоков, будут поспешными. Без данного элемента нельзя оптимально выстроить производственный поток с точки зрения сокращения длительности цикла и затрат на его функционирование. Как организовано обучение этому элементу в Объединенной авиастроительной корпорации?
Цель и задачи обучения
Цели обучения в нашей корпорации полностью совпадает с философией производственной системы Тойота – создание среды, обеспечивающей стабильное и беспрерывное выполнение производственных операций без лишней нагрузки на персонал и оборудование. Мы стараемся изменить менталитет сотрудников нашей Компании в части формирования желания по поиску и устранению потерь в повседневной работе.
Задачи обучения:
- Научить выявлять все виды потерь в условиях действующего производства;
- Научить разрабатывать оперативные планы мероприятий по минимизации/устранению потерь.
Если дополнительной задачей ставить рост производительности, то необходимо определить «узкие» места в производственном процессе, так как скорость потоков будет определяться пропускной способностью именно «узких» мест. Затем, через использование элемента «Устранение потерь», (подчеркиваем: без значительных материальных вложений!) «узкое» место расшивается, что позволяет влиять на скорость всего потока, следовательно, увеличить производительность и выработку на одного рабочего. Обращаем внимание: вопрос о значительных вложениях, например, закупке более производительного оборудования подымается, только если после устранения потерь в зоне «узкого места» производственного потока мы не достигли необходимых параметров по производительности, а также если коренная причина низкой пропускной способности относится к глубокому моральному или физическому износу оборудования.
Мы знаем, что решив поставленные перед нами задачи, мы сможем
- повысить качество выполняемой работы;
- привить бережное отношение к материально-технической базе предприятия;
- увеличить количество предложений по улучшениям;
- создать предпосылки к устойчивому росту производительности труда путем расшивки «узких мест».
Программа обучения
Программа обучения элементу «Устранение потерь по каждому рабочему месту» в ПАО «ОАК» состоит из пяти пунктов:
- теория;
- деловая игра;
- практика по выявлению, фиксации и систематизации потерь на одном рабочем месте в условиях действующего производства;
- разработка планов мероприятий по минимизации/устранению потерь;
- защита у руководства предприятия разработанных планов мероприятий и обоснование предполагаемого эффекта от реализации с учетом понесенных затрат на реализацию.
Рассмотрим содержание каждого пункта программы обучения.
1. Теория
В своей практике мы часто сталкиваемся с тем, что персонал предприятий, в том числе и руководители, не видят или предпочитают не замечать потери, так как уже привыкли работать в подобных условиях и это считается нормой.
Поэтому первоначально мы рассказываем, что:
1.1 Прибыль = Объем продаж * (Цена единицы продукции – Себестоимость ее изготовления),
а основная задача производственного персонала – это выпуск продукции в необходимом количестве с потребительскими свойствами, полностью удовлетворяющими запросам потребителя, при минимально возможной себестоимости изготовления. Ценовое позиционирование, в данном случае, мы относим к задачам маркетологов.
1.2 Объясняем и показываем на примерах, что такое полезная и бессмысленная работа (виды работ см. Таблицу 1).
Таблица 1. Виды работ по степени их полезности
Виды работ / действий |
Отличительный признак |
Задача |
Полезная |
Работа/действия, добавляющие ценность объекту нашего труда |
Обеспечить максимальную занятость |
Вспомогательная |
Работа/действия, не добавляющие ценности объекту нашего труда в глазах потребителей, но необходимые для выполнения полезной работы |
Максимально минимизировать |
Вредная, потенциально опасная организация производственного процесса |
||
МУДА
|
Работа/действие, потребляющее ресурсы и время, но не добавляющая ценности объекту нашего труда в глазах потребителей. Любое мероприятие, которое не приносит дохода – безсмысленная работа. |
Полностью исключить |
МУРА |
Неравномерная интенсивность труда/ «рваный» темп работы, при выполнении операций технологического процесса. Может привести к браку при резком переходе с минимального темпа на максимальный и простоям при обратном процессе. |
При отсутствии возможности исключения, обеспечить плавные переходы от минимального темпа на максимальный и наоборот |
МУРИ |
Запредельная интенсивность труда и критические режимы работы оборудования по сравнению с расчетной/технически обоснованной нагрузкой в течение длительного временного промежутка. Превышение интенсивности труда и производительности, не подкрепленное технологией и нормативами, приводит к браку, внеплановым ремонтам, травматизму и т.п. |
Полностью исключить, путем автоматизации и механизации выполняемых работ, а также перераспределения объемов работ между рабочими и оборудованием |
1.3 Рассказываем про восемь видов потерь присутствующих на любом предприятии:
- исправление дефектов;
- перепроизводство;
- лишняя обработка;
- лишняя транспортировка;
- лишнее хранение;
- ожидание;
- лишние передвижения;
- избыточные отходы.
Очень важно в процессе обучения показывать видео и фотоматериалы по каждому виду потерь на производстве, поскольку часто руководители не воспринимают привычные действия или ситуации в качестве потерь. Только после непредвзятого взгляда со стороны у руководителей начинает меняться восприятие, проводятся аналогии с демонстрируемыми потерями на других предприятиях и недостатками собственного производственного процесса.
1.4 Рассказываем о 12 видах потерь в рабочем процессе, которые неизбежны при бездумной организации рабочей зоны (см. Таблицу 2).Это позволяет более детально взглянуть на технологический процесс, сопоставить уровень квалификации рабочего, оценить организацию рабочего пространства. Поэтому в рамках обучения мы дополнительно напоминаем о принципах и содержании работ по системе 5S (см. Таблицу 3).
Таблица 2. 12 видов потерь в рабочем процессе
-
№
Вид потери
Отличительный признак
1
Обе руки не заняты
В процессе от начала до завершения операции обе руки оказываются не заняты по причине машинного времени и т.д.
2
Одна рука не занята
Одна рука выполняет действия, в то время как другая рука не занята (Идеалом является одновременное выполнение действий обеими руками).
3
Остановка действий по выполнению операций
Не происходит правильного и стабильного повторения операций (Остановка действий после выполнения каждой операции).
4
Множество лишних действий при выполнении операции
При выполнении операции действия работника, вызываемые размещением деталей и его местоположением относительно изделий, инструмента, оснастки, органов управления оборудованием, не сведены к минимуму.
5
Перекладывание из рук в руку
Работник берет деталь, которую собирается устанавливать, и затем перекладывает ее в другую руку.
6
Лишние перемещения
По причине далекого нахождения деталей и инструментов работник совершает передвижения на 1 шаг и более. (Идеалом является полшага вправо/влево)
7
Повороты большой амплитуды
Оптимальная амплитуда поворотов для работника – в пределах 450.
8
Отсутствие комбинаций действий
Выполняя одно действие, работник не производит никакого другого действия.
9
Отсутствие интуиции, сноровки и т.д.
Отсутствие навыков в работе, что приводит к ее переделыванию.
10
Необходимость тянуться за ….
Работнику приходится тянуться, чтобы взять деталь и т.д.
11
Необходимость нагибаться за ….
Работнику приходится нагибаться, чтобы взять деталь и т.д. (детали, рабочее место и т.п. расположены слишком низко)
12
Бессмысленность самих действий
Необходимо пересмотреть цель выполняемой операции и ликвидировать повторяющиеся и ненужные действия.
-
Принцип
Содержание работы
1. Удаление ненужного
(Кампания Красных Ярлыков).
Все предметы разделяются на три категории: ненужные, ненужные срочно и нужные.
Ненужные удаляются.
Ненужные срочно располагаются на определенном удалении от рабочего места или хранятся централизованно.
Нужные предметы сохраняются на рабочем месте.
2. Рациональное размещение.
По отношению к нужным предметам и предметам ненужным срочно вырабатываются и реализуются решения, которые обеспечивают:
-
быстроту, легкость и безопасность доступа к ним;
-
визуализацию способа хранения и контроля местонахождения нужного предмета;
-
свободу перемещения, эргономику производственной среды.
3. Уборка, устранение неисправностей.
-
поддержание чистоты на рабочем месте, уход за оборудованием, инструментом;
-
выявление и ликвидация источников загрязнения;
-
выработка правил проведения уборки, чистки оборудования, смазки, проверки.
4. Стандартизация
Фиксация правил в виде стандартов, максимальная визуализация (рисунки, схемы, указатели, цветовое кодирование), визуализация контроля нормального состояния и отклонений. Стандартизация и унификация всех обозначений, рационализация носителей информации (материал, способ нанесения надписей, защитные покрытия), мест их размещения и крепления.
5. Дисциплина и совершенствование
Закрепление сфер ответственности за каждым работником (объекты внимания и основные обязанности по их поддержанию в нормальном состоянии). Выработка у персонала правильных привычек, закрепление навыков соблюдения правил.
-
- Исправление дефектов – заливаем в чайник не кипяченую воду, а при приготовлении чая не доводим ее до кипения.
- Перепроизводство – добавляем в чай сахар, несмотря на то, что клиент не заказывал сладкий чай; готовим три чашки чая вместо двух заказанных.
- Лишняя обработка – кипятим один литр воды, вместо необходимых 200 мл.
- Лишняя транспортировка – носим воду, чай и т.п. с разных столов, расположенных на удалении друг от друга.
- Лишнее хранение – показываем, что для приготовления двух стаканов чая мы храним несколько пачек чая и сахара.
- Ожидание – бесцельно стоим, пока чайник закипит, все действия выполняем последовательно.
- Лишние действия – три раза добавляем чай в заварную емкость, размешиваем сахар в два этапа и т.п.
- Избыточные отходы – демонстративно выливаем большие остатки заваренного, но не использованного чая из заварной емкости.
- умение видеть все виды потерь в условиях производственного процесса (процесс приготовления чая);
- умение проводить хронометраж действий работника – делить все действия на элементы (умение видеть в технологической операции переходы), поэлементно фиксировать затраченное время;
- умение систематизировать собранную информацию в процессе хронометража. В процессе анализа отделять бессмысленную работу от полезной работы (работы, добавляющей ценности продукту в глазах клиента);
- умение формировать диаграммы «спагетти», наглядно показывающие транспортировку необходимых ингредиентов и движения работка в процессе приготовления чая;
- умение разрабатывать планы мероприятий по исключению бессмысленной работы и минимизации вспомогательной;
- умение разрабатывать эскизы целевой организации рабочей зоны по приготовлению чая;
- умение определять ожидаемый эффект от реализации мероприятий, направленных на исключение/минимизацию потерь.
Рис. 1. Пример диаграмм по систематизации потерь в рабочем процессе
При выявлении потерь данные систематизируются для упрощения их обработки (пример диаграммы приведен на рисунке 1). Последующий анализ данной диаграммы позволяет определить потенциал роста производительности на конкретном рабочем месте за счет исключения бессмысленной работы и минимизации вспомогательной. По данным компании «Тойота» только рациональная организация рабочей зоны с последующей работой по системе 5S позволяет повысить производительность на 15-20%.
Таблица 3. Принципы и содержание работ по системе 5S
2. Деловая игра
Деловая игра позволяет на бытовом примере закрепить полученные знания по выявлению и устранению потерь. Бытовой пример берется не случайно, он позволяет исключить личные амбиции, связанные с зоной своей ответственности на производственной площадке, и показать, что потери могут быть везде, нужно научиться их видеть, а затем исключить или минимизировать путем реализации мероприятий, не требующих значительного времени, сил и финансовых вложений.
В нашем случае в качестве бытового примера мы рассматриваем процесс приготовления чая, где демонстрируем следующие восемь видов потерь на предприятии:
В процессе деловой игры сотрудники приобретают ценные навыки:
Обращаем внимание, что процесс приготовления чая происходит два раза – второй раз после разработки и реализации планов мероприятий по устранению потерь. Мы наглядно показываем, каким может быть эффект при правильной организации производственного процесса: если первый раз нам потребовалось для приготовления двух стаканов чая 17 минут, то после реализации мероприятий только шесть. Процесс обучения представляет симбиоз индивидуальной и коллективной работы. Каждый обучаемый проводит индивидуальные замеры, классифицирует потери, составляет диаграмму «спагетти», разрабатывает план мероприятий по улучшениям, подготавливает эскиз целевой организации рабочей зоны. После чего мы коллегиально создаем единый лист хронометража, отделяем и классифицируем потери, разбираем допущенные ошибки и неточности, считаем преодолеваемые расстояния, разрабатываем и реализовываем сводный план по улучшениям/устранениям потерь, спорим, рассуждаем, проводим аналогии с реальным производством. Пытаемся избавиться от стереотипа, что без значительных финансовых вливаний невозможно получить рост производительности и снизить себестоимость.
В процессе деловой игры наша главная задача – раскрыть и направить творческий потенциал обучаемых руководителей в конструктивное русло.
3. Практика по выявлению, фиксации и систематизации потерь на одном рабочем месте в условиях действующего производства.Никакая деловая игра не может в полной мере научить видеть и, главное, устранять потери. Теоретическое обучение в сочетании с деловой игрой позволяет взглянуть на производственный процесс под необходимым углом – это инструмент, который работник может использовать в своей повседневной работе только при наличии желания. Поэтому в качестве проверки того, насколько эффективно данным инструментом могут пользоваться обучаемые, мы реализуем практический этап в условиях действующего производства.
Фото: Практический этап обучения выявлению потерь
По сути, обучаемые руководители проводят фотографию рабочего дня одного производственного рабочего, но есть и ряд обязательных дополнительных наблюдений, сопровождаемых фотоотчетом выявленных несоответствий и объектов для последующего улучшения:
1. Проводиться обследование организации рабочего места / рабочей зоны по системе 5S с заполнением соответствующего чек-листа и фото фиксацией текущего состояния.
Фото: Чек-лист по обследованию рабочего места |
|
|
|
Фотографии выявленных несоответствий системы 5S в части хранения инструмента, технологической оснастки и уборки оборудования
|
|
2. Предварительно изучается планировка рабочей зоны, подготавливается эскиз фактической рабочей зоны. Подготавливаются диаграммы перемещений рабочего и товарно-материальных ценностей (Диаграммы «спагетти»);
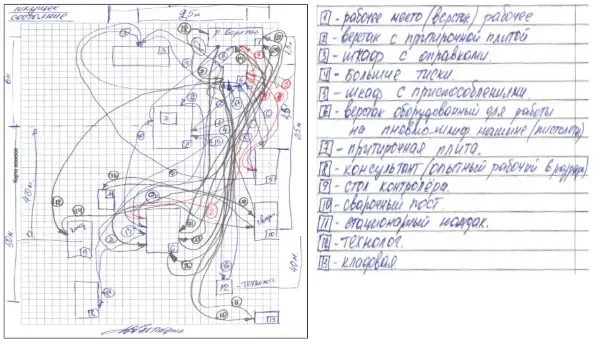
3. Проводиться оценка степени взаимодействия рабочего с непосредственным руководителем. Происходит фиксация:
- когда, в каком виде, на какой временной период выдаются задания на выполнение работ;
- как осуществляется оценка выполненной работы по объёму, качеству и срокам;
- как непосредственный руководитель контролирует ход выполнения выданного задания, как решает возникающие у рабочего в процессе работы оперативные вопросы.
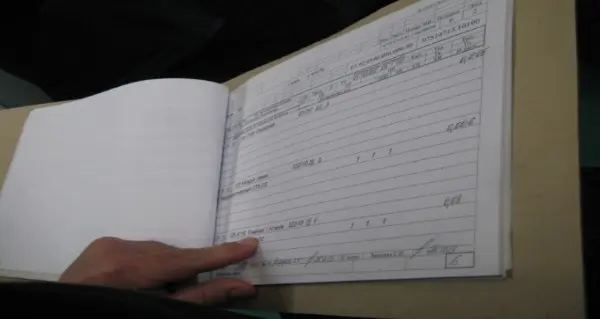
5. Сопоставляется фактическая интенсивность труда и нормативная / плановая при выполнении задания выданного непосредственным руководителем;
6. Фиксируются нарушения/предпосылки для возникновения производственного травматизма и чрезвычайных происшествий, связанных с промышленной безопасностью;
Фото: предпосылок для возникновения производственного травматизма. |
|
Отсутствуют замки на крюках |
Отсутствуют рукоятки |
|
|
7. Осуществляется фиксация физического состояния инструмента и технологического оснащения используемого в работе. Отдельное внимание обращается на дату аттестации.
Фото: Фиксация технического состояния технологического оснащения
4. Разработка планов мероприятий по минимизации / устранению потерь
По результатам проведённой фотографии рабочего дня и выполненных наблюдений каждый обучаемый руководитель предлагает и обосновывает мероприятия по устранению / минимизации потерь. В процессе разработки планов мы часто сталкиваемся с тем, что у многих руководителей есть сложности с формулировкой мероприятий, назначением ответственных за реализацию и сроков выполнения. Поэтому на примере предлагаемых мероприятий со стороны обучаемых руководителей мы рассказываем о технологии постановки целей SMART. Согласно которой цели наших мероприятий должны быть: конкретны, измеримы, достижимы, значимы и ограничены во времени (табл. 4).
Таблица. 4. Расшифровка аббревиатуры SMART
Буква |
Значение на английском |
Перевод |
S |
Specific |
Конкретная, определённая. |
M |
Measurable |
Измерима, поддающаяся измерению. |
A |
Attainable |
Достижима. |
R |
Relevant |
Значима, амбициозна. |
T |
Time-bounded |
Ограничена во времени. |
Мы учим:
- правильно ставить цели;
- подкреплять достижимость поставленных целей разработанными мероприятиями;
- пользоваться методом: «5 Почему?».
Пять «Почему?» — это эффективный инструмент изучения причинно-следственных связей, лежащих в основе коренных причин возникновения потерь. Пяти вопросов, как правило, достаточно для выявления источника проблемы. Несмотря на название, для поиска причин каждого конкретного несоответствия может потребоваться как меньшее, так и большее количество вопросов. Метод «5 почему?» не исключает выстраивания «дерева» причин, поэтому подход схож с методом, используемым в причинно-следственной диаграмме Исикавы («Рыбья кость»). Нам важно не найти виновного, а выявить и в последствии устранить с помощью предлагаемых мероприятий именно системную причину, так как решение промежуточных проблем, без внимания к первопричине, всё рано приведет к повторному возникновению потерь.
В конечном итоге каждый обучаемый по итогам четырех этапов обучения подготавливает следующий пакет документов:
- перечень выявленных и систематизированных потерь в рабочем процессе, а так же общезаводских (системных) потерь присущих любому предприятию;
- оцифрованную полезную работу, выполняемую рабочим и цифровую детализацию бесполезной работы;
- фото отчёт текущей организации производственного процесса в части последующей реализации его улучшений, исключения рисков возникновения производственного травматизма и выпуска не качественной продукции;
- экспертную оценку эффективности оперативного управления рабочими в части поддержания интенсивности труда, качества выполняемой работы, соблюдения правил охраны труда и внутреннего трудового распорядка, а так же оперативности решения возникающих проблем в процессе выполнения сменных заданий;
- план мероприятий по устранению/минимизации выявленных потерь и рисков;
- экспертную оценку эффекта вызванного реализацией каждого мероприятия направленного на устранение/минимизацию потерь.
Фото: Защита у руководства предприятия разработанных планов мероприятий
На данном этапе важно закрепить мысль, что работа не делается ради самой работы – конечная цель это добавочная стоимость придаваемая продукту в процессе работы над ним на конкретном рабочем месте. При этом необходимо сопоставлять понесённые затраты и получаемую добавочную стоимость, за которую клиент готов заплатить. То есть на данном этапе мы подходим к оценке эффективности разработанных планов мероприятий путём сопоставления возможных выгод и затрат. Определяется приоритетность реализации подготовленных мероприятий по соотношению трех критериев: время реализации, затраты на реализацию, ожидаемый эффект, при этом ряд мероприятий могут быть отклонены, как неэффективные.
Рис. 2. Определение приоритетности реализации подготовленных мероприятий
Защита работ является обоюдно ценным этапом для топ-менеджеров предприятия и обучаемых руководителей более низкого уровня.
Топ-менеджеры оценивают потенциал своих подчинённых и возможный эффект от реализации планов мероприятий по устранению / минимизации всех видов потерь; видят текущее, а не показное состояние производственной площадки; и узнают изнутри недостатки протекающих процессов и их взаимное влияние.
В то время как обучаемые:
-
приобретают навыки:
- по выявлению потерь в условиях действующего производства;
- разработки оперативных планов мероприятий по минимизации/устранению потерь;
- общения с топ-менеджерами через «защиту» разработанных мероприятий, в том числе в процессе ответов на задаваемые вопросы со стороны руководителей;
- привлекают дополнительное внимания топ-менеджеров к существующим проблемам и последствиям от их возникновения;
- по результатам защиты кандидатуры обучаемых рассматриваются на предмет включения в кадровый резерв.
Заключение
В чем же заключается не только сиюминутная, но и стратегическая выгода обучения выявлению потерь на рабочих местах?
По итогам обучения руководители начинают пересматривать окружающую их действительность с точки зрения наличия и оценки величины потерь, предъявляют требования по минимизации/устранению потерь в работе к себе и своим подчиненным.
Согласно экспертной оценке рост производительности за счет устранения потерь составил от 25 до 60% (диапазон представлен из 60 работ обученных начальников цехов).
Однако, запуская программы обучения, важно помнить одно: без поддержки топ-менеджмента предприятий подобный потенциал роста эффективности может так и остаться нереализованным. Если мероприятия окажутся не выполненными и люди столкнутся с безразличным отношением своих руководителей, эффект в целом будет отрицателен, а второй раз «расшевелить» персонал будет гораздо сложнее, в ряде случаев – и вовсе невозможно.
Юрий Максимов,
заместитель директора развития ПС П
ПАО «ОАК» увеличило количество поставленных в год воздушных судов с 53 до 159. Среднегодовой темп роста составил 20%. К концу 2015 г. в состав корпорации вошли 15 авиаремонтных заводов, таким образом, в П
Задать вопросы Юрию и узнать больше об опыте ОАК вы сможете на третьей конференции «Повышение эффективности
Комментарии